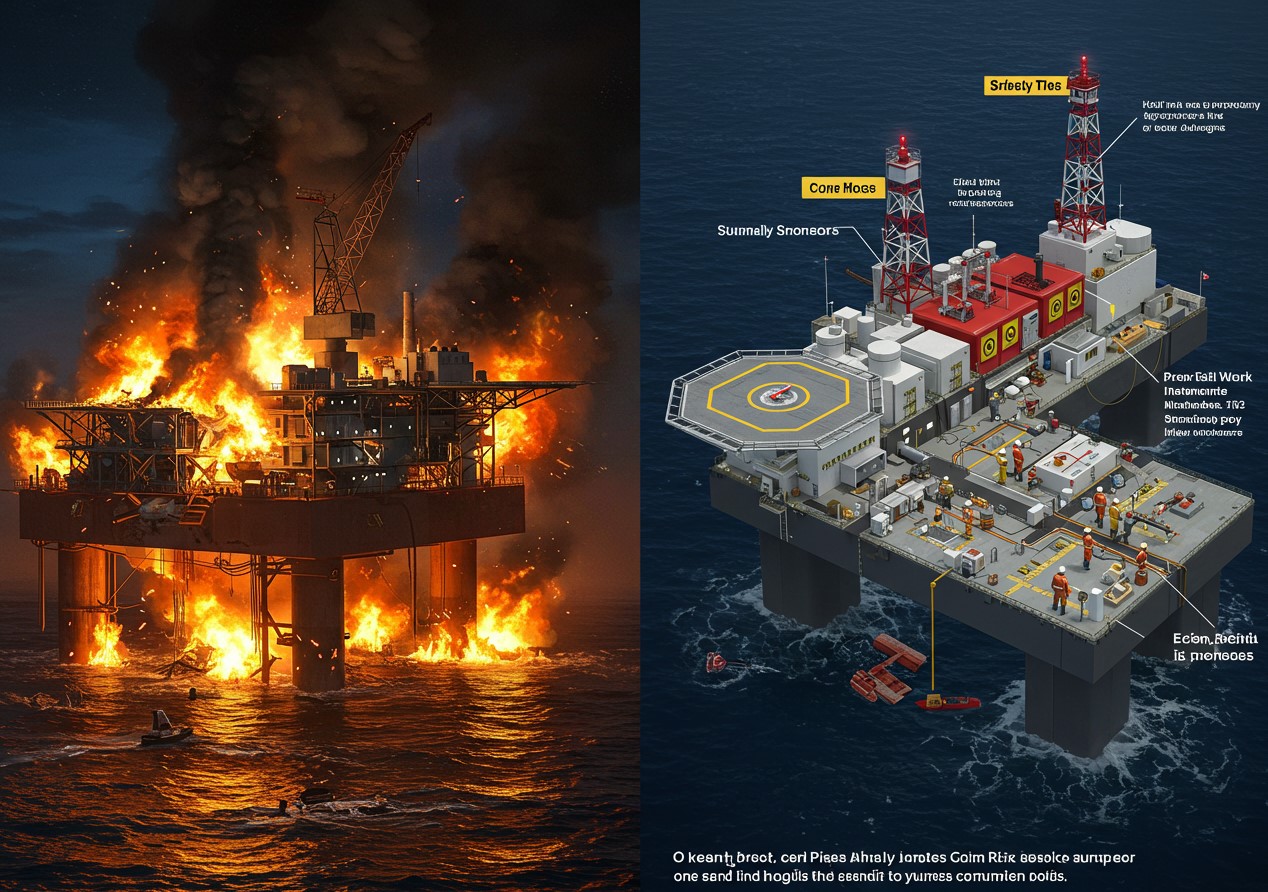
El desastre de Piper Alpha (6 de julio de 1988) sigue siendo un punto de inflexión en la historia de la seguridad industrial. Con 167 víctimas mortales y pérdidas económicas millonarias, este accidente en la plataforma petrolera del Mar del Norte expuso fallas sistémicas en la gestión de riesgos que, trágicamente, siguen siendo relevantes hoy.
Este artículo, basado en el análisis detallado de Álvaro Conde (CST – CONSERTO S.A.S.), reconstruye los eventos críticos que llevaron a la catástrofe, utilizando metodologías como el BowTie y el análisis de barreras fallidas. Su objetivo es claro: convertir el dolor en aprendizaje, identificando lecciones que toda organización industrial debe internalizar para evitar repetir errores fatales.
Piper Alpha: Breve Contexto
Piper Alpha era una de las plataformas más productivas del Mar del Norte en los años 80, diseñada originalmente para procesar petróleo pero adaptada posteriormente para manejar gas natural. Esta modificación no evaluada rigurosamente fue el primer eslabón en una cadena de fallos:
-
Falta de análisis de riesgos: No se consideraron escenarios de explosión, solo incendios.
-
Barreras incompletas: Muros resistentes al fuego, pero no a explosiones.
-
Gestión fragmentada: Sistemas de permisos de trabajo y comunicación deficientes.
El evento desencadenante fue una fuga de gas propano debido a una válvula de alivio mal asegurada durante labores de mantenimiento. Lo que siguió fue una secuencia devastadora:
-
Explosión inicial en el Módulo C (22:00 hrs).
-
Fallos en cascada:
-
Sistema de agua contra incendios desactivado manualmente (para proteger buzos).
-
Plataformas vecinas (Tartan y Claymore) continuaron bombeando combustible al incendio.
-
Estructura colapsó tras múltiples explosiones, arrastrando al mar el módulo habitacional (zona de evacuación).
-
Lecciones Clave: ¿Por qué Fallaron las Barreras?
El análisis con metodología BowTie reveló que, de 9 barreras identificadas (3 preventivas, 6 mitigadoras), 8 fallaron. Estas son las lecciones críticas:
1. Cultura de Seguridad vs. Producción
-
Error clave: Priorizar la producción sobre protocolos. Ejemplo:
-
Se reinició una bomba en mantenimiento (sin válvula de alivio) para evitar parar la planta.
-
Los permisos de trabajo no se comunicaron entre turnos.
-
-
Lección: La seguridad debe ser responsabilidad directa de la alta gerencia, no solo del área de HSE.
2. Independencia y Redundancia de Barreras
-
Barreras dependientes: El sistema de permisos (conductual) y el aislamiento seguro (socio-técnico) fallaron simultáneamente.
-
Lección: Las barreras deben ser independientes y auditables (ej.: hardware activo + protocolos automatizados).
3. Diseño Inherentemente Seguro
-
Falta de «defensas en profundidad»:
-
Pisos con rejillas (para evitar acumulación de líquidos) fueron cubiertos con goma, creando piscinas de combustible.
-
Módulos habitacionales no tenían rutas de evacuación alternas.
-
-
Lección: Las modificaciones deben evaluarse con herramientas como HAZOP y LOPA.
4. Preparación para Emergencias
-
Simulacros inexistentes: Nadie anticipó que el helipuerto sería inaccesible por humo.
-
Lección: Los planes de evacuación deben probarse en escenarios realistas (no solo teóricos).
Conclusión: De la Tragedia a la Acción
Piper Alpha nos dejó un legado imborrable: la seguridad no es un costo, es una inversión. Como señala el informe Cullen:
«La suma y calidad de nuestras contribuciones individuales a la gestión de la seguridad determina si nuestros compañeros viven o mueren» (Brian Appleton, Asesor Técnico de la Investigación).
Recomendaciones para la industria actual:
-
Adoptar enfoques sistemáticos: Integrar BowTie, LOPA y análisis de barreras en la toma de decisiones.
-
Auditorías rigurosas: Evitar la «falsa sensación de seguridad» con evaluaciones imparciales.
-
Cultura de aprendizaje: Documentar y compartir incidentes menores para prevenir catástrofes.